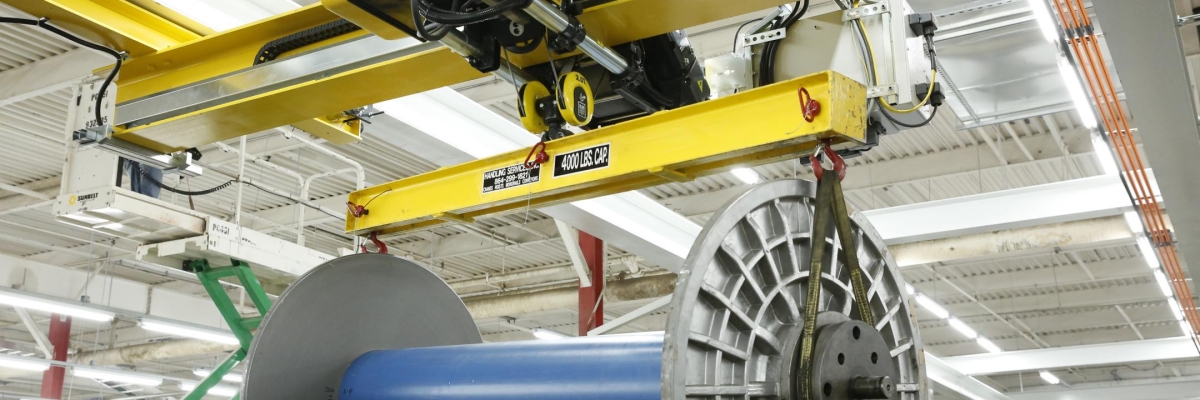
The Application: Low-cost labor in developing nations makes textile manufacturing a low margin business. So, when Taiwan-based Everest Textiles announced plans to open a U.S. sports fabric weaving plant in North Carolina that would employ more than 600 U.S. workers, a focus on efficiency was key – from construction of the facility, all the way to how yarn rolls would be moved and loaded into looms.
While the mid-Atlantic region was once home to many textile operations, globalization and low-cost labor in Asia had forced nearly all the region’s textile mills to move operations overseas. Everest’s plans to set up a weaving operation in the U.S. required scale and efficiency to profitably supply top brands with the latest fabrics. As a result, the Everest Textile facility incorporated more than 600 looms when it first opened in late 2017, with hundreds more planned as operations scaled up.
As a crane system designer and engineer with more than 25 years of experience, Mike assumed that a C-track festoon crane would likely meet Everest’s needs. But when he visited the old industrial mill Everest planned to renovate, there was a problem.
The Challenge: “The ceiling was low,” Mike said. While the height was 20 feet, there was also a 24-inch reduction due to water piping and other conduit running across the ceiling. Once Mike saw that, he knew that a normally less expensive festoon crane would prove to be just the opposite, leading to a cascade of unexpected costs, from expensive structural changes to the building to additional heating, ventilation and air conditioning costs. The reason, Mike said, is due to the design of C-track festoon cranes.
Traditional C-track festoon crane systems are supplied with power via cables secured in small trolleys that run inside a track. With this design, the cables hang below the bridge girder, typically by several feet. In facilities that offer plenty of overhead clearance, festoon cabling causes no issues. In facilities with lower ceilings or limited clearance, however, Mike said even a few inches can mean the difference between a workable solution, and a crane that breaks down from festoon cable snagging on pipes, wiring, shelving and equipment.
The Solution: Facing the issue of limited clearance, HSI turned to R&M Materials Handling for an NRGmaster crane, which Mike said is the ideal solution for retrofit facilities like Everest Textile’s where height restrictions make installing a standard festoon crane cost prohibitive.
“The NRGmaster has a clean design and it’s very easy to install,” Mike said. “And R&M is just a good experience. Anytime we have the choice, we choose R&M.”
The design of the NRGmaster crane incorporates an energy chain power system that requires no additional ceiling or overhead clearance. Its power and control cables are enclosed in a flexible “energy chain,” which rests in a guide channel that is fastened to the web of the bridge girder. The free end of the chain bends into a U-shape and connects to the hoist tow arm, while the other end fastens to the channel. This enables the chain to roll back and forth inside the guide channel as the hoist travels from one side of the bridge girder to the other.
While HSI installed an NRGmaster at Everest Textile with 2-ton capacity, Mike said he’s used the crane in heavier industry applications because it can be ordered with a capacity up to 80 tons. The NRGmaster can also accommodate two hoists per bridge beam and, Mike said, it’s quiet.
“That makes a big difference for safety in a busy plant,” Mike said. “I could stand next to you and have a quiet conversation when it’s running and we would have no problems.”
HSI also outfitted the NRGmaster with a Racon 3 radio control unit. A handheld remote control, Mike said the Racon 3 dramatically improves safety and productivity over older cranes that have to be operated from a fixed point, like an overhead cab, while requiring a second person to be in communication with the crane operator about load movement and placement.
The Racon 3 has an ergonomic design that provides operators with one-hand usability through the integration of a joystick element. Providing a comfortable grip, crane operators can focus completely on the load while controlling the crane from the safest location with no restriction of a fixed-length push button controller cable.
“It has just a few controls so it’s a simple design that more people can operate,” Mike said. “It’s also safer because you’re on the floor and can see the load at all times with no line-of-sight restrictions.”
The Results: Since the install, Nick said the crane has saved Everest time and led to high levels of productivity as yarn beams are switched in and out of looms. In fact, Everest is so pleased with the setup that plans call for a second NRGmaster to be installed when production begins in a mezzanine level of the plant.