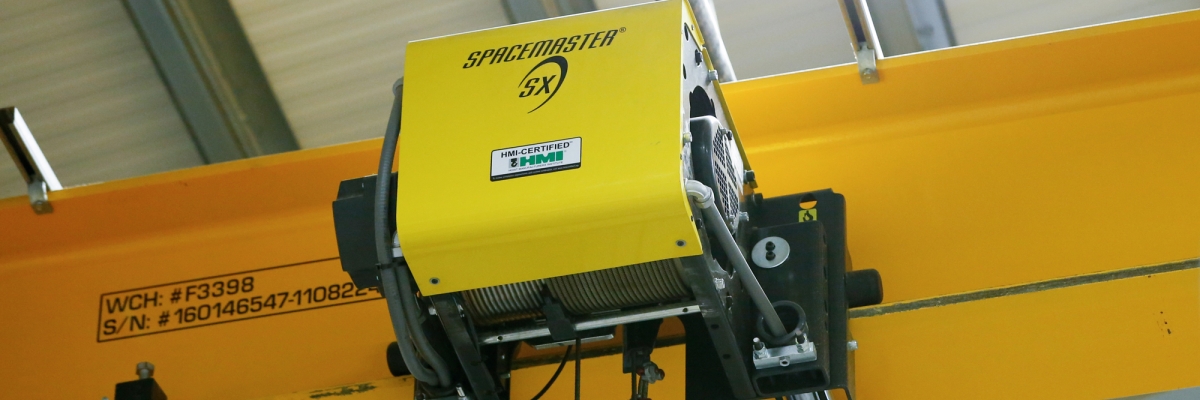
The Application: As Anchorage, Alaska’s oldest utility, Anchorage Municipal Light & Power (ML&P) has been generating the electricity for Alaska’s largest city for more than 85 years. Servicing a 20-square-mile area that includes some of the city’s oldest neighborhoods, along with commercial, university and medical customers in the downtown and midtown business districts, ML&P has an incredible responsibility: Without its continuous and reliable generation and distribution of electricity, modern life in this sub-arctic climate would not be possible.
To ensure that electricity generation for the region is both consistent and efficient, ML&P undertook an expansion in 2014 of its George M. Sullivan Plant 2, the utility’s primary electric generation plant, installing two natural gas-fueled, General Electric combustion turbines and one Siemens steam turbine capable of producing 120 megawatts. The $314 million project also required the construction of a natural gas compression building where two, 10-ton natural gas compressors are used to increase the pressure of incoming natural gas. The importance of these compressors, and the equipment used to service them, is difficult to overstate.
“The turbines can only operate within a strict range,” explains Nat Lewis, ML&P Plant 2 Superintendent. “We are at the end of the straw, in terms of the natural gas line, so depending on a variety of factors, including temperature, our gas pressure can swing substantially.”
The Challenge: Residents of Anchorage, Alaska, live in a region that is both beautiful and unforgiving. While nature lovers flock to this city, they also must endure a sub-arctic climate where it’s not uncommon for temperatures to dip into the negative teens during the depths of winter. That means the loss of electricity can be catastrophic. ML&P’s electric generation and distribution ensures that homeowners, businesses and industrial facilities in the area can remain habitable, even during the coldest and darkest days of Alaska’s legendary winters.
Yet twice a year, ML&P is required to “take down” half of its electricity generation at Plant 2 to service all the equipment and ensure that it continues to operate at peak efficiency. That means disassembling and lifting out the natural gas compressors. The only way to do that is with a powerful hoist and crane system that can both handle the 20,000 pounds of each compressor, and operate in an environment where potential sparks must be eliminated for risk of explosion.
The challenge this creates for ML&P is clear. Without a functioning gas compressor, and a reliable crane system to service the compressor, electricity generation for more than 24,000 residential customers, 6,400 commercial customers, and the region’s joint Army and Air Force base, Joint Base Elmendorf-Richardson, can’t be generated.
Facing the challenge of determining the best option for a critical piece of equipment, ML&P turned to Washington Crane & Hoist for the design and installation of a crane system. In business since 1975, Washington Crane & Hoist prides itself on providing innovative overhead material handling equipment, parts and service throughout the Western United States.
ML&P’s Plant 2 expansion presented a challenge, said Cody Baggett, Washington Crane’s Alaska Branch service manager. The project required meeting significant tolerances to operate in the compressor building. While the structure is fairly open, the building does have pipes and conduit running across the ceiling that limit hoist options. The other, and most significant challenge, Baggett said, was identifying an explosion-proof crane that could operate in the compressor building environment while delivering unquestionable reliability. When all the factors were combined, Baggett said it quickly became apparent the type of crane that would be used.
The Solution: “Reliability was definitely a key factor for this job,” Baggett said. “We put this project out to bid and R&M was the clear winner. They always come back with a great price and great service.” Working with R&M Materials Handling, Washington Crane determined the best choice for its client was the the Spacemaster® EX. A wire rope hoist, the Spacemaster EX combines the explosionproof, protective features necessary for operation in a hazardous location, with the lifting and headroom capacity that would meet the physical demands of the ML&P’s compressor building.
The Spacemaster EX is the hazardous location version of the industry-leading Spacemaster SX hoist. It carries a Class I, Division 2 explosion-proof rating for groups C and D and temperature class 3. It also features non-sparking options that make it the ideal choice for hazardous conditions. Bronze-coated hooks, brass wheels and brass drop lugs on the trolley act as spark prevention.
Like the Spacemaster SX, the EX features an innovative design that includes a large drum diameter, which enables both the lowest headrooms and best wheel loads in the industry, while providing near-true vertical lift with single reeving. Employing a large diameter drum also makes it possible for exceptional hook approaches and lift heights.
Washington Crane outfitted the Spacemaster EX with an explosion-proof radio control unit. The explosion-proof bellybox radio controller improves crane safety and productivity by allowing operation from the floor with clear sight lines to the load. This enables much greater efficiency compared to older cranes that must be operated from a fixed point, like an overhead cab or fixed length pendant controller, while requiring a second person to be in communication with the crane operator about load movement and placement.
Because R&M hoists and crane systems are so reliable and the maintenance required on its equipment is so minimal, Baggett said Washington Crane specified the Spacemaster EX with complete confidence.
The Results: Since completion of the Plant 2 expansion, ML&P has retired four older generating units at the plant, slashed its emissions (nitrogen oxide by 97 percent, carbon monoxide by 80 percent and carbon dioxide by 30 percent), and saved $8.4 million annually on generation costs. It has also been able to reliably service its gas compressors twice annually, without incident, ensuring that electricity generation for the region has remained uninterrupted, even in the darkest, coldest days of Alaska’s long winters.